Fillable Printable Detailed Construction Scope of Work Template
Fillable Printable Detailed Construction Scope of Work Template
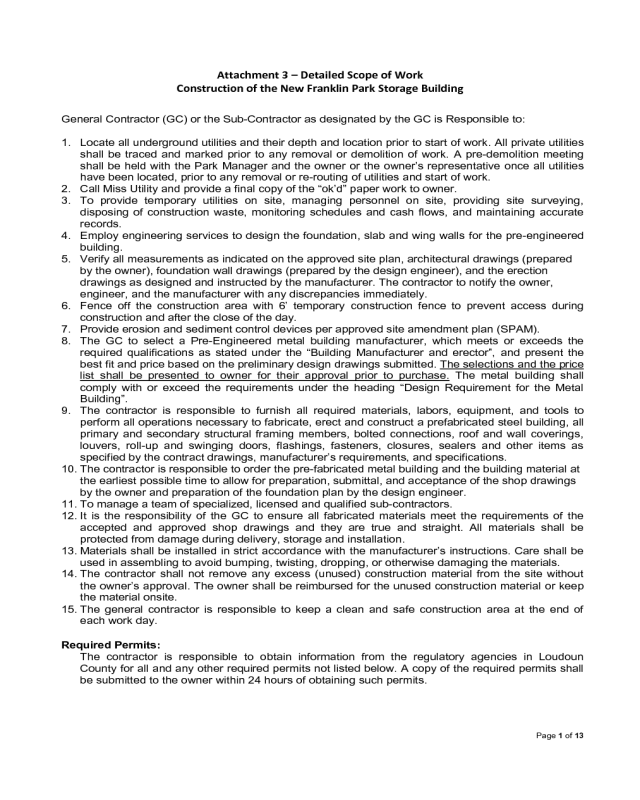
Detailed Construction Scope of Work Template

Attachment 3 – Detailed Scope of Work
Construction of the New Franklin Park Storage Building
Page 1 of 13
General Contractor (GC) or the Sub-Contractor as designated by the GC is Responsible to:
1. Locate all underground utilities and their depth and location prior to start of work. All private utilities
shall be traced and marked prior to any removal or demolition of work. A pre-demolition meeting
shall be held with the Park Manager and the owner or the owner’s representative once all utilities
have been located, prior to any removal or re-routing of utilities and start of work.
2. Call Miss Utility and provide a final copy of the “ok’d” paper work to owner.
3. To provide temporary utilities on site, managing personnel on site, providing site surveying,
disposing of construction waste, monitoring schedules and cash flows, and maintaining accurate
records.
4. Employ engineering services to design the foundation, slab and wing walls for the pre-engineered
building.
5. Verify all measurements as indicated on the approved site plan, architectural drawings (prepared
by the owner), foundation wall drawings (prepared by the design engineer), and the erection
drawings as designed and instructed by the manufacturer. The contractor to notify the owner,
engineer, and the manufacturer with any discrepancies immediately.
6. Fence off the construction area with 6’ temporary construction fence to prevent access during
construction and after the close of the day.
7. Provide erosion and sediment control devices per approved site amendment plan (SPAM).
8. The GC to select a Pre-Engineered metal building manufacturer, which meets or exceeds the
required qualifications as stated under the “Building Manufacturer and erector”, and present the
best fit and price based on the preliminary design drawings submitted. The selections and the price
list shall be presented to owner for their approval prior to purchase. The metal building shall
comply with or exceed the requirements under the heading “Design Requirement for the Metal
Building”.
9. The contractor is responsible to furnish all required materials, labors, equipment, and tools to
perform all operations necessary to fabricate, erect and construct a prefabricated steel building, all
primary and secondary structural framing members, bolted connections, roof and wall coverings,
louvers, roll-up and swinging doors, flashings, fasteners, closures, sealers and other items as
specified by the contract drawings, manufacturer’s requirements, and specifications.
10. The contractor is responsible to order the pre-fabricated metal building and the building material at
the earliest possible time to allow for preparation, submittal, and acceptance of the shop drawings
by the owner and preparation of the foundation plan by the design engineer.
11. To manage a team of specialized, licensed and qualified sub-contractors.
12. It is the responsibility of the GC to ensure all fabricated materials meet the requirements of the
accepted and approved shop drawings and they are true and straight. All materials shall be
protected from damage during delivery, storage and installation.
13. Materials shall be installed in strict accordance with the manufacturer’s instructions. Care shall be
used in assembling to avoid bumping, twisting, dropping, or otherwise damaging the materials.
14. The contractor shall not remove any excess (unused) construction material from the site without
the owner’s approval. The owner shall be reimbursed for the unused construction material or keep
the material onsite.
15. The general contractor is responsible to keep a clean and safe construction area at the end of
each work day.
Required Permits:
The contractor is responsible to obtain information from the regulatory agencies in Loudoun
County for all and any other required permits not listed below. A copy of the required permits shall
be submitted to the owner within 24 hours of obtaining such permits.
Attachment #3 – QQ-01765
Detailed Scope of Work
Page 2 of 13
1. Site permit and zoning, by owner; fees are waived by Loudoun County Department of Building
and Development.
2. Code modification/waiver for the second bathroom requirement by IPC, by owner.
3. Building Permit/s, including the demolition of the building, and foundation wall are the General
contractor’s responsibility; fees are waived by Loudoun County Department of Building and
Development.
4. Building permit to re-build the pre-engineered building, the foundation, and the wing walls are
the responsibility of the GC; Fees are waived by the Loudoun County Department of Building
and Development.
5. Electrical permit and plans (if required by Building Development), is the contractor’s
responsibility, fees are waived by the Loudoun County Department of Building and
Development.
6. Mechanical permit and plans (if required by Building Development), contractor’s responsibility,
fees are waived by the Loudoun County Department of Building and Development.
7. Plumbing permit and plan (if required by Building Development), contractor’s responsibility,
fees are waived by the Loudoun County Department of Building and Development.
8. Health department approval, well and septic connections, contractor’s responsibility, fees are
waived. Contractor is required to check with the department to obtain information on the
required plans and permits, if any.
Submittals:
1. Submit a construction schedule and the sequence of work to the owner; please note the county
holiday schedule when preparing the construction schedule. Once approved, any change to
the schedule shall be approved in advance by the owner.
2. Provide the list of professionals and the subcontractor’s, once selected, to the owner.
3. Submit the Architectural plans as part of the plan submittal; Prepared by the owner.
4. Complete sets of instructions for field procedures for erection and adjustment prior to
construction to the owner.
5. The manufacturer shall supply the contractor with Pre-engineered shop drawings; the said
drawings shall show the dimensions, complete erection drawings with the proper identification
and assemblage of the building component, all relevant details, along with the calculations
booklet sealed and signed by an engineer registered in the Common Wealth of VA. Owner’s
approval is required prior to any submittal to the county or the design engineer. A copy of the
said material shall be provided to the owner.
6. The manufacturer’s shop drawings shall include the,
Product data and samples (6” long x 24” width) on all building skin and roof systems,
window systems, and doors shall be approved by the owner prior to ordering. A copy of
the product data and samples, as required, to be submitted to the owner.
Product data and samples (6” long x 24” width), on all color and material samples of all
finished surfaces including the interior and exterior materials shall be approved by the
owner prior to ordering. A copy of the product data and samples, as required, shall be
submitted to the owner.
7. Submittal of the calculation’s booklets and shop drawings, from the manufacturer of the pre-
fabricated buildings, to the pre-listed structural engineer for the design of the foundation, slab
and foundation wing wall/s. Owner’s approval is required prior to submission to engineer. A
copy of all calculations, plans, and shop drawings shall be submitted to the owner.
8. Structural foundation drawings and calculations shall include the foundation design based on
the reactions submitted by the manufacturer, slab and reinforcement design, anchor bolt, base
plates, the lift slab, and the foundation wing wall/s design along with all pertinent details, and

Attachment #3 – QQ-01765
Detailed Scope of Work
Page 3 of 13
shall be sealed and signed by the design engineer registered in the Common Wealth of VA.
These plans shall be submitted along with Architectural plans, prepared by the owner, and the
sealed and signed manufacturer’s erection drawings and calculations plans, the electrical plans
signed by licensed electrician or certified as directed by the Building and Land Development,
mechanical plans signed by licensed mechanical contractor or certified as directed by the
Building and Land Development, and the plumbing plans signed by licensed plumbing
contractor or certified as directed by the Building and Land Development, to the Loudoun
County Department of Land and Building Development to obtain the building permit by GC. It
is the responsibility of the engineer of the record to verify that the loading criteria
defined on the order document is adequate and modify as needed.
9. The floor slab shall be placed over properly compacted subgrade with required thickness of
gravel base with Poly Vapor Barrier and perimeter insulation as shown on the plans. The
surface of the slab shall be sloped to drain outward at the bay garage doors.
10. Provide rigid insulation under the slab 2’-0” wide minimum to meet the minimum R-10
insulation value.
11. The thickness of the storage slab and the location of the control joints shall be per engineer’s
approved drawings.
12. The finished surface of the slab shall be hard, smooth, skid resistant concrete on areas that are
not to be covered.
13. A portion of the slab labeled as “Lift area” is to be designed as a heavy duty reinforced
concrete slab suitable for industrial use is required (shown on the building plans as the “lift
area”). The slab shall be designed to support the weight of the lift plus 12,000 lb. the lift is
supported at four (4) points. Each leg of the lift is welded to a, provided, 4”x6” plates and to be
attached to slab with 2 bolts. The exact dimensions and the full weight shall be furnished to the
contractor and engineer prior to preparation of the design.
Note: MEP plans and permit, except for Plumbing Ground work, may be submitted to Loudoun
County at a later time, if permitted by Building Development Department. GC or
contractor to allow time to obtain all permits.
14. Drawings on all electrical systems including light fixtures, electrical panel board, wiring,
transformers, and circuiting, grounding, exhaust fans, powered roof fans and Carbon monoxide
exhaust systems shall be prepared and signed by a licensed electrical contractor or certified as
required by the Building Development. Prior owner’s approval is required.
15. Drawings on all Mechanical systems, HVAC system, and ventilation system shall be prepared
and signed by a licensed mechanical contractor or certified as required by the Building
Development. Prior owner’s approval is required.
16. Drawings on all plumbing systems, riser diagrams, pipe connections and sizes, materials and
fixtures color and specifications shall be prepared and signed by a licensed plumbing
contractor or certified as required by the Building Development. Prior owner’s approval is
required.
17. Coordinate all MEP plans with the Architectural and manufacturer’s plans.
Site Work:
All site/grading and erosion and sediment control device placement shall be in accordance with
the approved lot grading plans, and all applicable codes adopted and enforced by Loudoun
County.

Attachment #3 – QQ-01765
Detailed Scope of Work
Page 4 of 13
Clearing & Grubbing:
All vegetation and debris within the limits of construction, except as designated to remain, shall
be cleared, grubbed, removed, and disposed of. All vegetation and objects to remain shall be
protected.
Demolition:
Demolish and remove the entire existing barn building including the concrete slab, the existing
foundation wall and footings, if any.
Support the cut, if necessary to avoid slope failures. Any damage to the slope and the cut is the
responsibility of the contractor.
Construction Debris:
All construction derbies may be placed in containers and removed from the site. The dump
fees are waived on county projects.
Construction Equipment:
1. All construction equipments shall be secured locked and grounded after each work day.
2. Provide the Project Manager with a list of all construction equipment that remain on site at each
construction stage.
Foundation and wing Walls:
1. The foundation and wing walls shall be constructed per the approved engineered drawing/s.
2. The walls shall be designed to support the lateral earth pressure from the soil and the surcharge
from the new parking lot and driveway along the length of the walls (depending on the location
of the walls). The wall shall also support all reactions from the steel frames supplied by the steel
manufacturer.
3. Provide water proofing behind the foundation and foundation wing walls.
4. Provide minimum 12” of gravel behind the walls.
5. Provide draintile along the length of the walls, day light the ends to proper designated drainage
areas away from the building.
6. Provide guardrail to the height and at locations as required by IBC 2009 and approved plans.
Guardrail
1. Guardrail shall be provided, on top of the wall where there is an elevation difference of greater
30”.
2. The guardrail height shall be 42” minimum.
3. The guardrail shall be made of pressure treated, SYP #2 or better.
4. The posts shall be 6x6 pressure treated @ 5’-0” o.c maximum.
5. The top rail shall be 2x6 minimum applied flat, SYP #1 or better. The edges of the top rail shall
be rounded and smooth without splinters.
6. The top surface shall be smooth and without checks and splinters.
7. The balusters shall be 2x2 pressure treated at 4” O.C. maximum.
8. The side rails shall be 2x4, applied flat, pressure treated #2 minimum.
9. All connections shall be stainless steel or hot dipped galvanized except for ½” or larger bolts.
Applicable Codes and Standards:
1. The building and its components shall comply with USBC 2009, and all referenced codes and
standards as amended.
2. All Concrete work shall comply with latest applicable, adopted and referenced ACI 350 code.
3. All Masonry work shall comply with latest applicable, adopted and referenced ACI 530 code.
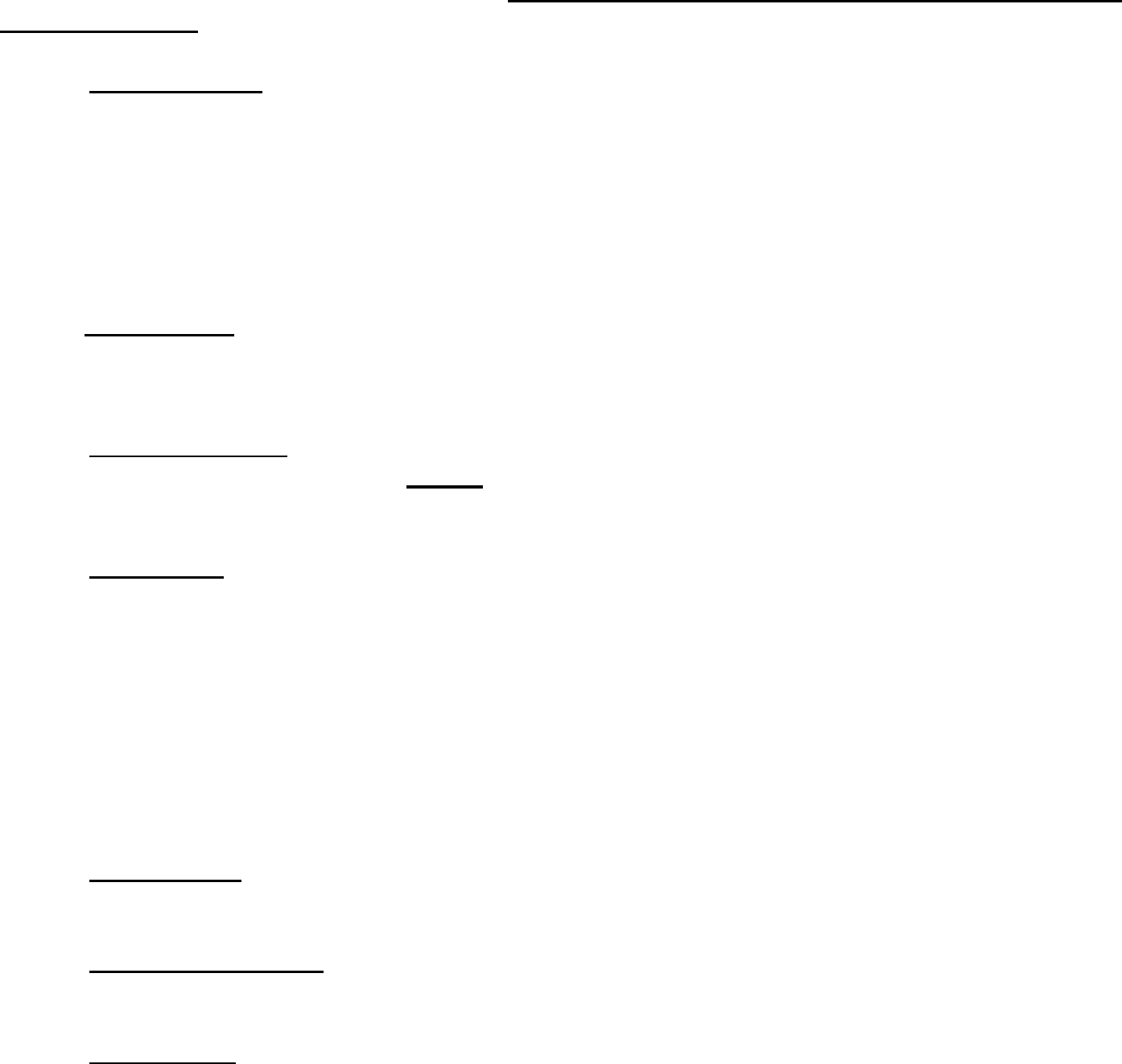
Attachment #3 – QQ-01765
Detailed Scope of Work
Page 5 of 13
4. All Steel work shall comply with latest applicable, adopted and referenced AISC code, 13
th
edition, ASD method.
5. Cold-Formed steel structural members shall be designed in accordance with the latest edition of
AISI “Specifications for the Design of Cold-Formed Steel Structural Members”.
6. All interior cold formed galvanized steel frame work shall be in accordance with AISI-NAS.
Design Requirements for the Prefabricated Steel Building:
Design shall be based on Allowable Stress Design (ASD) and shall comply with the
following minimum design requirement. These values may be changed by the engineer of
the record only.
1. Design Codes:
Design shall be in accordance with USBC 2009, and all referenced material codes (ACI,
NDS, ACI-530, AISC, AISI, etc.), and shall comply with all applicable local amendments,
if any.
All structural steel sections and welded plate members shall be designed in
accordance with the latest edition of the AISC, “Specification for the Design,
Fabrication, and Erection of Steel for Buildings” and IBC.
2. Dead Loads:
The dead load shall be the weight of the Metal Building System and as determined by
the system manufacturer.
3. Collateral Loads:
The collateral load shall be 10 psf or as shown on the contract drawings. Collateral
Loads shall not be applied to the roof panels.
4. Live Loads:
Roof Live Load:
The building system shall be capable of supporting a minimum uniform live load
of 30 psf, non-reducible. The live load shall be applied to the horizontal roof
projection.
Floor Live Load:
The building concrete slab shall be capable of supporting a minimum uniform live
load of 100 psf.
5. Snow Loads:
The design ground snow load shall be 30 psf non-reducible.
6. Importance Factors:
I
s
=
1.00 & I
w
= 1.00
7. Wind Loads:
The design wind speed for the metal building system shall be based on 90 mph,
3 second gust, exposure “C”.
All interior walls shall be metal studs galvanized G60 minimum or better and be
designed for 5 PSF lateral load.
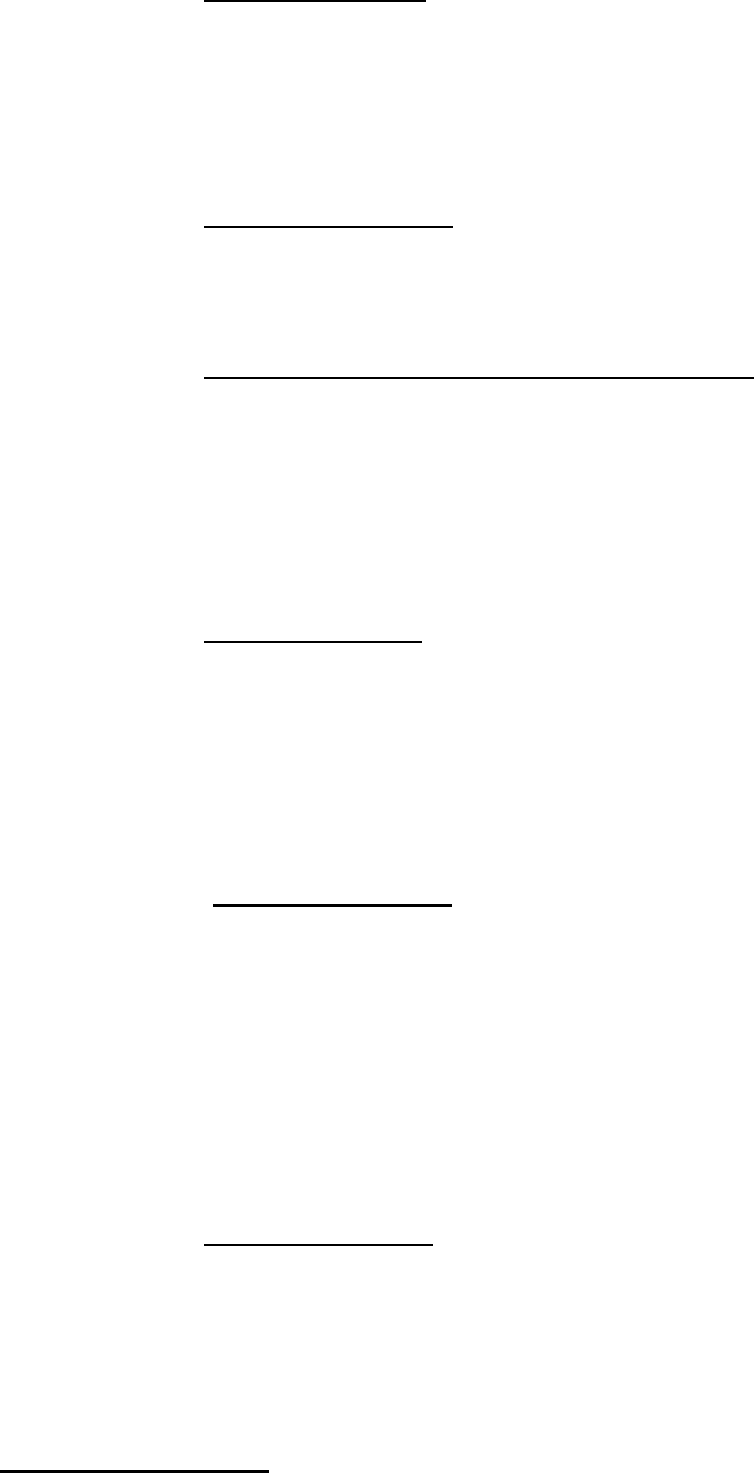
Attachment #3 – QQ-01765
Detailed Scope of Work
Page 6 of 13
8. Seismic Loads:
Seismic load shall be determined based upon a response acceleration factors S
s
=0.164,
S
1
= 0.052
Seismic Design Category “C”
Seismic Site Class “D”
9. Rainfall Intensity:
All exterior gutters and downspouts shall be designed in accordance with the provisions
of the code having jurisdictions.
10. Deflections shall be limited as follows:
The Live load Deflection of the primary and the secondary members shall be per latest
applicable ASCE7 standard.
Roof Members Not supporting Ceiling l/240.
Roof Members supporting plaster ceiling l/360.
Exterior Walls and Interior partitions l/240
11. Code Analysis:
Occupancy Category is designated as II
Use Group “S-1”.
Type of Construction “IIB”
Occupancy load (Reduced) to 15 (total) per waiver approved by Loudoun County
Building Development Dated, November 16, 2012. A copy of approval is attached.
12. Thermal Effects:
Standing Seam roof panels shall be free to move in response to the expansion and
contraction forces resulting from a temperature variation.
The building is cold and not insulated, except for the office areas as shown on the
drawings.
Assembly to permit movement of components without buckling, failure of joint
seals, and undue stress on fasteners; insulation shall be provide to underside of
the roof to prevent excessive expansion and contraction.
13. Site Conditions:
The following site features and adjacent structures must be considered in the design.
The building will be adjacent to a hill, approximate drop in elevation 5’ to 6’. There are
few trees in the back of the building. The closest building to the new structure is about
50’ away.
Storage building:
The Storage building is separated into three areas; a 54’x28’ a 70’x53’ and 55’x17’ areas. The total
area of the building is calculated to be 6157 sq. ft.
The building will house a very small amount of Hazardous materials; however, the amount is
well below the limits set for “H” use group and specified in IBC table 307.1 (1). A full listing of
these materials may be provided to the contractor upon request. The owner is responsible to
provide an adequate and NFPA approved storage area to store these materials.
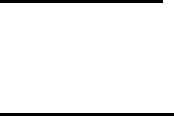
Attachment #3 – QQ-01765
Detailed Scope of Work
Page 7 of 13
Shop Coating:
1. Galvanized Structural Framing,
All structural framing members and all other steel accessories that are galvanized and
chemically treated for paint adherence and which are not factory color coated shall receive one
(1) coat of Galvanized Metal Primer conforming to Federal Specification TT-P-641b, Type II, or
equivalent, then painted with two (2) coats of Industrial Enamel within forty eight (48) hours
after the prime coat is applied.
2. Structural Framing Not Galvanized,
All structural framing members and miscellaneous steel accessories which are not galvanized
shall be cleaned to remove all dirt, grease, oil, and loose mill scale, given one (1) shop coat of
zinc chromate iron oxide primer conforming to Federal Specification TT-P-636b, and field
painted, prior to erection, with two (2) coats of Industrial Enamel approved by the District.
3. Exposed Galvanized Surfaces.
All roof and wall panels, flashing, trim, and other exposed galvanized steel surfaces shall be
factory color coated with a twenty (20) year guarantee.
4. Ventilators, Louvers and Doors,
Any required ventilators, louvers, and doors shall first receive one (1) coat of Galvanized Metal
Primer, then be factory color coated with two (2) coats of Industrial Enamel as manufactured by
Ditzler, DuPont, Pittsburgh Paints, or approved equal, within forty eight (48) hours after the
prime coat is applied.
5. Color and Paint Schedule,
All colors for all finish painted surfaces shall be per owner’s approval unless otherwise specified.
Warranty:
1. Building manufacturer shall provide manufacturer's standard material warranty in writing and
present to owner.
2. Metal building contractor shall provide a workmanship warranty for a minimum period of 20
years in writing and present to owner.
Building details:
1. The building is a combination of Gable Symmetrical continuous frame building (roof ridge at the
center) and a mono-slope Gable frame building with straight roof rafters and straight columns
without center or intermediate supports.
2. The length of the overhang depends on the cost; required overhang between 2’ minimum
and 4’ maximum.
3. (Option A) Provide roof extension 19’ (17’ of roof and 2’ of overhang minimum.), as part of the
prefabricated steel building, over the Art Center storage area. Maintain the slope from the
interior support to the exterior wall.
(Option B) As a cost saving option, the Art Center storage area may be designed as part of the
steel framed building with an interior support system to be provided on the wall between the Art
Center Storage area, if needed, and the Main Storage area.
4. The building width and length shall be measured from outside to outside face of the sidewall
girts.
5. The eave height shall be measured from the bottom of the base channel to the intersection of
the lines representing the inside of wall covering and the roof covering.
6. Clear wall height shall be 16’-0” minimum.
7. The building shall be water and weather tight.
8. The building frame shall be plumb and in-line to the specified spacing by the manufacturer’s
drawing.
9. Purlins and girts shall be plumb and to the spacing specified by the manufacturer’s specification.
Attachment #3 – QQ-01765
Detailed Scope of Work
Page 8 of 13
10. Shall have adequate ridge vents, soffit vents, and mechanical roof vents (powered), to allow for
proper air circulation and air exchange.
Connections:
The frame erection and all connections shall be in complete accordance with the
Manufacturer’s drawings and specifications. It is the responsibility of the erector to replace or
repair any damaged connection per manufacturer’s or the engineer’s recommendation.
damage.
1. All connections shall be zinc coated steel with a zinc chromate finish except for anchor bolts and
exposed sheet metal screws. Exposed sheet metal screws shall be stainless steel.
2. All shop connections shall be by welding in accordance with the AWS “Standard Code for
Welding in Building Construction” the welders and the welder operators shall have been pre
qualified and certified as required in the code.
3. All field connections shall be bolted. The bolts shall be machine bolts conforming to latest ASTM
Specification A-307 for all secondary framing members, and ASTM Specification A-325 for
bearing frame end walls and for main frame connections and as shown on the drawings.
Primary Framing Members:
All framing members shall be shop fabricated for field assembly. The steel sections shall
conform to requirements of ASTM A36. All framing members shall carry an easily visible
identifying mark, stamped, stenciled or painted to facilitate erection.
1. All primary rigid frames shall be welded built-up “I” or hot rolled sections.
2. The columns and the rafters may be straight.
3. All base plate splice and flanges shall be shop fabricated to include bolt connection holes. Webs
shall be shop fabricated to include bracing holes.
4. The connections for purlins and girts shall be by means of welded clips. Refer to manufacturer’s
drawings for location.
5. The roof erection shall be in complete accordance with the manufacturer’s Erection Manual. Any
deviation from this manual that results in roof damage is the responsibility of the erector to
replace and/or repair the damage per manufacturer’s specification or engineer’s
recommendation.
Base Support:
1. A continuous member shall be provided to support and attach the base of the wall covering. The
base support shall be galvanized base channel attached to concrete floor with hooked anchor
bolts. Close all gaps between the base support and concrete with appropriate material to
prevent any air and water penetration.
2. The base support shall be minimum of 6” above the finished grade.
Secondary Framing Members:
1. Purlins and Girts shall be cold formed “Z” sections with stiffened flanges.
2. Diagonal bracing may be used in the roof, sidewalls and gable walls.
Roof and Wall Covering Materials:
1. All sidewall panel lengths shall be continuous from sill to eave line.
2. Extend the wall covering 2” beyond the base angle and provide base trim and flashing.
3. All end wall panels shall be beveled cut in the field by the erector.
4. The wall panels shall be pre-painted finish Galvalume steel panels 24 gauge, conforming to
ASTM 792.
5. The wall covering and color to match the existing “Art center’s” exterior wall covering or as
directed by the owner; Prior owner’s approval is required. The walls are not insulated unless

Attachment #3 – QQ-01765
Detailed Scope of Work
Page 9 of 13
noted otherwise on the plans. The owner is requesting a quote for insulated walls after
contract award.
6. The roof covering shall be standing seam roof panels. Insulated to prevent excessive expansion
and contraction due to temperature changes.
7. The standing seam roof panels shall be UL-90 rated, roll-formed, 24 gauge pre-painted
Galvalume with minimum yield of 50 Ksi. All Galvalume panels shall conform to requirements of
ASTM-792. Prior owner’s approval is required.
8. The panel size and the height of the seams shall resemble the existing “Art Center” roof or as
directed by the owner; Prior owner’s approval is required.
9. All panels shall be factory cut at both ends. The panel installation shall start from one end and
finish at the other.
10. Steel ridge cap shall be minimum 26 gauge galvanized steel, factory color coated, to match the
roof panels and shall be provided along the roof ridge.
11. Provide Adhesion Mounting snow and ice guards throughout the length of the roof.
Framed Openings:
All framed openings shall be adequate to support all design loads and specified deflections and
shall be fully trimmed and flashed. All framing members exposed to weather shall be galvanized
steel.
Sealant and Closures:
1. The corrugations of the roof and wall panels shall be filled with pre-formed rubber, neoprene or
Polyethylene closures along the eave, ridge rake and base.
2. All gutter and downspout joints, ridge flashing laps, doors, windows and louvers shall be sealed
with color to match trim (as approved by owner), Butyl rubber base caulk.
Gutters and Downspouts :
1. Eave gutters shall be roll-formed, free of waviness and any imperfections. All gutter sections
shall be securely fastened and sealed at end laps. The outside face of the gutter shall be 26
gauge minimum thickness factory painted GALVALUME with supports at every 24” O.C.
2. Downspouts shall be 4” x 4” roll formed box sections. Use matching straps to secure the
downspouts to the building wall. Kickouts shall be provided on each downspout.
3. The downspouts shall drain to an approved drainage area.
4. The minimum spacing of downspouts shall be 25’ or as recommended by the engineer.
Flashing and Trim:
1. Flashing and/or trim shall be provided at the rake, corners, eaves, framed openings, and
wherever necessary to provide weather and water tightness and a finished appearance.
2. All flashing shall be manufactured from pre-painted Galvalume steel.
3. All trims shall be pre-painted Galvalume, color to be selected by the owner, 24 gauge or vinyl.
Light gauge cold formed members:
1. The design of cold formed steel members shall be in accordance with appropriate AISI sections
and shall also comply with IBC 2009, section 2210.
2. All cold formed interior wall shall be designed for a minimum 5 psf lateral loads in addition to all
Cold formed other applicable loads.
3. steel framing members shall have a legible label with the following minimum information;
Manufacturer’s identification
Minimum base steel thickness
Minimum coating designation
Minimum yield strength
Attachment #3 – QQ-01765
Detailed Scope of Work
Page 10 of 13
4. Cold formed steel shall have a metallic coating complying with ASTM A 1003 and Minimum of
G60 in accordance with ASTM A653.
5. The cold formed steel framed wall shall be anchored to slab or foundation.
6. The cold formed steel members shall be connected per engineered drawings.
7. All cold formed sections shall be manufactured by precision
8. All members shall be straight and free of any defects.
9. Do not proceed with manufacturing prior to review of shop drawings
10. Submit samples 6” long x full panel width showing the metal gauge and panel profile.
11. The panel manufacturer shall have a minimum 10 years of experience in manufacturing roofing.
12. The installer shall have a minimum of 5 years experience in installation of metal roofing in
similar size and scope.
13. The panels and flashing shall be protected and properly packaged to prevent any damage
during the transportation.
14. Store panels and flashing in a dry and safe environment.
15. All dimensions shall be verified prior to fabrication.
16. All panels shall be 24 gauge structural steel.
17. The panels shall be smooth, the final finish shall be per owner’s requirement.
18. Any request for alternate system shall be submitted to project manager in writing at least 10
days prior to ordering the materials.
19. All screws shall be plated steel or stainless steel. They shall have a combination EPDM gasket
and painted flange to match the color of the roofing.
20. The flashing shall be shop fabricated from a material that is a same thickness and finish as the
corrugated panels.
21. Dispose of debris from jobsite.
22. All extra materials shall be transferred to the owner if the owner request it.
Painting:
1. All uncoated structural steel shall be cleaned of all foreign matter and loose scale in accordance
with SSPC-2 and given a one mil coat of red oxide primer. The primer shall meet or exceed the
performance requirements of Federal Specifications TT-P-636.
2. All roof and wall panels, flashing, trim, and other exposed galvanized steel surfaces shall be
factory color coated with 20 year warranty.
3. Furnish primer for touch-up or field painting.
4. The base metal shall be pre-treated and then primed with epoxy type primer for adhesion and
corrosion.
5. All structural framings which are not galvanized, their Surfaces shall be clean and dry free of
dirt, grease, oil, wax, mildew, loose paint, rust and mill scale. The rusty metal surfaces should
be sandblasted or treated, before priming with one shop coat of zinc chromate iron oxide primer,
meeting the Federal Specification TT-P-636.
Windows:
1. Frames and doors shall be installed in accordance with plans and shop drawings in a rigid,
substantial manner and shall be weather tight, waterproof, square, plumb and level.
2. All windows double hung, polished aluminum finish, 3’-0”x5’-0”, color to match the trim and as
approved by the owner. The glazing to be double insulated sealed glass. All windows shall be
furnished complete with hardware, and full screen. Windows shall be self flashing to wall panels.
Window locations are as shown on the conceptual plans.
Personnel Doors:
1. Frames and doors shall be installed in accordance with plans and shop drawings in a rigid,
substantial manner and shall be waterproof, weather tight, square, plumb and level.
Attachment #3 – QQ-01765
Detailed Scope of Work
Page 11 of 13
2. All personnel doors shall be flush type, 3’-0” x 7’-0” x1 ¾” solid core steel door with no more
than 3/32” clearance from frames. Manufactured from 2 formed steel cover sheets, 20 gauge
thick, and reinforced with 20 gauge steel channels. The top and bottom edges of doors shall be
closed and reinforced with steel channel members extended full door width and welded full
width.
3. Each door unit shall be furnished with ½” high extruded aluminum threshold with sweep strip
and necessary fasteners.
4. All locksets shall be provided by the owner and shall be ADA approved.
Garage Doors:
1. Frames and doors shall be installed in accordance with plans and shop drawings in a rigid,
substantial manner and shall be water tight, weatherproof, square, plumb and level.
2. Curtains shall be galvanized steel and prime coated. The curtain shall be equipped with a full
length steel angle, securely fastened to the bottom of the curtain.
3. The guides shall be roll-formed of 13 gauge galvanized steel. Provide heavy nap stripping to
allow for rattle-free operations and to provide dust and weatherproofing.
4. All garage doors shall be 12’-0” tall x 12’-0” wide steel door roll up power operated.
5. All parts shall be given a factory applied rust inhibitive prime coat of paint. All scratches on the
primed surfaces shall be touched up after erection.
6. Door shall be electronically operated with manual override.
Interior Features:
1. The interior ceiling over the staff room # “101”, staff room # “102”, Storage room # “103”, and
the handicapped unisex bathroom shall be covered with corrugated metal roofing.
2. Provide interior covered ceiling with ½” gypsum board under the ceiling for room 101, 102, and
103 and also in the handicapped bathroom ceiling.
3. The clear finished ceiling height, in all finished areas, shall be 10’-0” minimum.
4. All walls to be covered with dry wall and per approved architectural plans. Prepare drywalls and
paint all walls per approved color by owner.
5. ½” gypsum board to be applied to both sides of the metal studs.
Interior Roof Ceiling Covering
1. Provide factory formed, unfinished and Lapp able corrugated metal roof. With 1” overhang.
2. Submit manufacturer’s specifications, standard profile sheet and product data sheets/brochure
to owners prior to ordering.
3. Provide shop drawings showing the roof plan and material type, and metal thickness. The
drawing shall distinguish between field and factory fabrication.
Bathroom:
1. All walls studs shall be 6” cold formed steel. Insulated R-30 minimum except as noted
otherwise.
2. All ceiling shall be designed as specified on the approved drawings, with R-11 minimum value.
3. Provide a unisex ADA accessible bathroom with sink (hot and cold water) and toilet. Reinforce
the wall behind the grab bars as required and as shown.
4. Provide VCT (Vinyl Composition Tile) tiles on to cover the bathroom floors.
5. Provide rolled VCT wall protection 4’-0” above the finished floor all around.
6. Provide VCT base molding 4” high from the finished floor on the perimeter walls.
7. All outlets in the bathroom shall be GFI.
8. Connection to septic system is required; length is as shown on the approved SPAM.