Fillable Printable Executive Summary - University of Pennsylvania
Fillable Printable Executive Summary - University of Pennsylvania
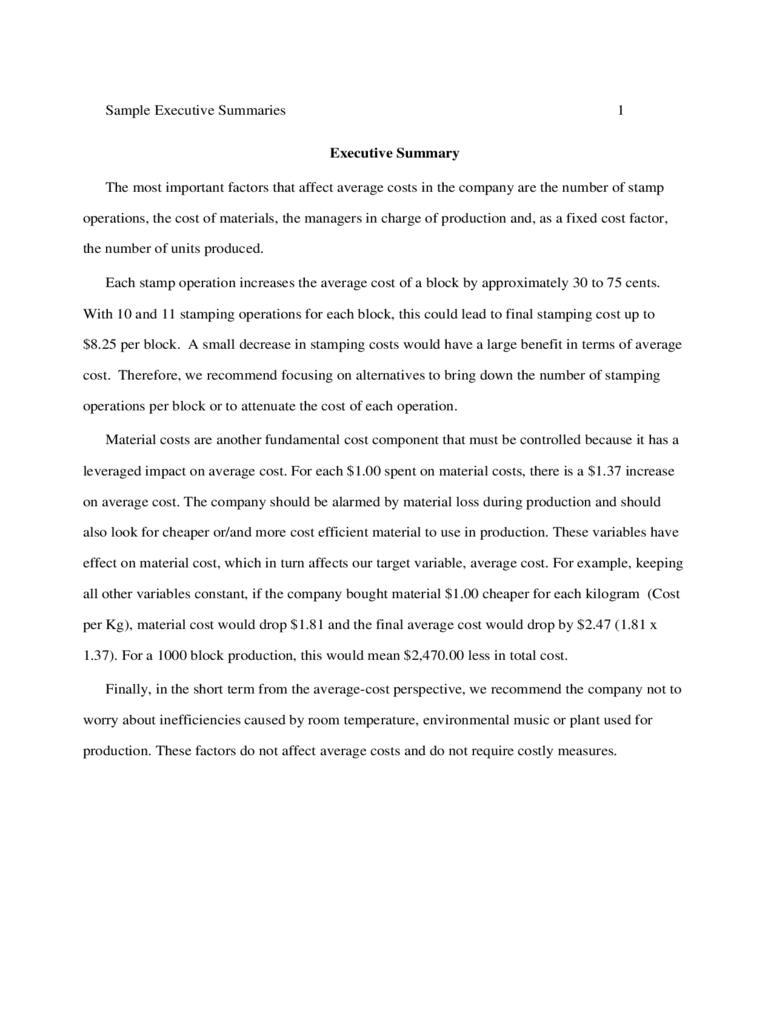
Executive Summary - University of Pennsylvania
Sample Executive Summaries 1
Executive Summary
The most important factors that affect average costs in the company are the number of stamp
operations, the cost of materials, the managers in charge of production and, as a fixed cost factor,
the number of units produced.
Each stamp operation increases the average cost of a block by approximately 30 to 75 cents.
With 10 and 11 stamping operations for each block, this could lead to final stamping cost up to
$8.25 per block. A small decrease in stamping costs would have a large benefit in terms of average
cost. Therefore, we recommend focusing on alternatives to bring down the number of stamping
operations per block or to attenuate the cost of each operation.
Material costs are another fundamental cost component that must be controlled because it has a
leveraged impact on average cost. For each $1.00 spent on material costs, there is a $1.37 increase
on average cost. The company should be alarmed by material loss during production and should
also look for cheaper or/and more cost efficient material to use in production. These variables have
effect on material cost, which in turn affects our target variable, average cost. For example, keeping
all other variables constant, if the company bought material $1.00 cheaper for each kilogram (Cost
per Kg), material cost would drop $1.81 and the final average cost would drop by $2.47 (1.81 x
1.37). For a 1000 block production, this would mean $2,470.00 less in total cost.
Finally, in the short term from the average-cost perspective, we recommend the company not to
worry about inefficiencies caused by room temperature, environmental music or plant used for
production. These factors do not affect average costs and do not require costly measures.
Sample Executive Summaries 2
Executive Summary
It is evident that a very large determinant of cost for the firm is the manager involved in the
product process. Gerry consistently produces runs more efficiently than any other manager. For our
sample, just changing the manager can result in a 24% change in total cost, from about $4400 to
$5400. At the same time it is worrying that there are such stark differences in working conditions
between the old plant and the new plant (in terms of breakdowns per unit, reworks, and temperature
variation). As a result it is hard to tell how well any of the old plant managers would be able to
perform if they moved to the new plant. If the firm can reduce the fluctuations, especially in
breakdowns/unit (which add a considerable $141 on average to each production run) and
temperature the firm might find improved performance among the managers in the old plant.
An analysis of the old plant finds that its workers must rework a lot of blocks - which in turn is
why the machine hours are so high with many breakdowns. All of this might be due to fluctuations
in temperature (which cause the computer-guided machinery to malfunction).
Going further, I recommend that the firm collect a larger data set in order to capture some of the
conditions not modeled so that the firm can get a better handle on costs. Some of the relationships
we were unable to understand for lack of data include whether or not a rushed and detailed job
impact costs. A larger data set might enable us to get a better idea of whether there are additional
costs involved. Other factors such as labor hours used, cost per kg, goal SD, and music were also
considered but were not found to be relevant having no measurable impact on cost.
In addition, I recommend that the company analyze its pricing so as to make good use of the
fact that it can handle variability in the job profile without affecting its cost structure. This could be
an excellent tool to use in marketing the product and creating a tiered pricing structure so as to gain
higher profits on products that customers value more (though the firm must be careful to first
understand the cost implications for rush vs. detail jobs).
Sample Executive Summaries 3
Executive Summary
I recommend the firm in the short run control three important factors to lower costs. First, there
should be a much better forecast of the amount of material required per block pre-machining. There
is wide variation in the amount of lost material per block and assuming a cost of $4/kg, this loss
typically contributes to about 20% of the average cost per block.
Second, manager Chris has been performing much better than average, saving about $4/block
or almost 8% of the average cost per block. The firm should analyze the factors for his success and
possibly train the other managers to implement these cost savings across the board.
Third, the firm should implement better climate control in the old plant. The costs in the old
plant are sensitive to the room temperature. If the temperature is at 65F instead of 75F, the costs are
on average higher by $3, 6.5 % of the average cost per block.
In addition, the model has a wide predictive range because of the limited number of data points
and the confounding present in the data. For example, the managers and the plants are
complementary. The firm should continue to randomly sample more production runs and
accumulate a richer collection of data, say 1000 runs. This should give rise to a more accurate
model and identify other factors that can be addressed in the long term. The model also shows that
labor hours are an important fraction of the costs and the firm could look at possible alternatives to
reduce the cost of labor (such as hiring more contract workers instead of permanent workers). In
summary, there is potential for significant cost savings that the firm can achieve by implementing
these changes.
Sample Executive Summaries 4
Executive Summary
I recommend that the firm enhance profitability by making its manufacturing process more
efficient and by marketing its service more effectively.
Manufacturing efficiency can lead to cost savings in three ways. First, breakdowns in the old
plant cost, on average, $190 per run. A1so, a breakdown is 4.3 times as likely in the old plant as it
is in the new plant. Since reducing breakdowns by 50% in a 100-unit run reduces costs by 5%,
exploring ways to do so are strongly recommended.
Second, manager productivity should be improved in the old plant. The average performance
difference between the best and the worst manager in the old plant is $4 per block, which is nearly
10% of the cost of the average block in a 200-unit run.
Third, temperature must be stabilized in the old plant since costs ramp up as the square of the
difference from 75 degrees. A ten-degree drop in temperature can increase costs by 10%. These
costs can be controlled by investing in climate control equipment for the old plant. Furthermore,
since manufacturing costs are lower in the old plant versus new plant by 5% for a 100-unit run,
efficient load optimization can yield better results.
Cost of detailed jobs and rushed jobs are irrelevant as chiseling is machine intensive and
stamping is labor intensive. Consequently, the firm can potentially reposition its marketing
strategy to emphasize detailing or rushing (but not simultaneously) versus the old chisel and stamp
positioning.
Sample Executive Summaries 5
Executive Summary
Our analysis of the firms production costs indicate a disconnect between the variables that the
customers control and the cost of the production output. In addition, the firm can optimize the use
of its managers and the temperature of its plants to reduce production cost and improve the bottom
line.
Five of the six customer specifications do not affect the costs of the order. In particular, items
such as rush, detail, and stamp do not contribute to the cost and therefore can be exploited to extract
the highest profit. Any premium charged for these specifications will directly contribute to the
margin of the production. For example, a 200-unit, detailed job and a 200-unit, rush job both cost
$41 per unit to produce. Charging a $10 premium for the rush job would not increase the cost but
would directly translate into profits.
Second, one of the firm’s managers, Chris, produces blocks at $5 less per unit than other
managers. We recommend that the firm benchmark Chris' methodology to extract an additional $5
per unit produced. On typical production jobs, this would represent approximately $8,000 to
$12,000 in cost reductions. Further, the fact that Chris’ lower costs are not directly related to other
variable costs indicates that his methodology is potentially transferable.
Finally, it is imperative for the firm to alter its cost structure around the features of the job
related to chisel, labor hours, material costs, breakdown/unit, temperature and manager. These
features directly affect the costs of production and should be the guiding metric for the firm’s cost
function.